Type of grinding wheel
TIME:
2022-05-17 15:53
Types of Grinding Wheels Grinding wheels generally combine abrasive grains with a special process, and then perform grinding, cutting, grinding, polishing, etc. on the workpiece, so the grinding wheels can be roughly classified from the perspective of bonding agents. Electroplated diamond grinding head is a general term for small shank grinding tools, which are used in electric grinders, hanging grinders, and hand drills. There are many types, mainly ceramic grinding heads, rubber grinding heads, diamond grinding heads, abrasive cloth grinding heads, etc. Through the understanding of the grinding wheel bond, it is easier to master the use of the grinding wheel, master the performance of the grinding wheel, and maximize the role of the grinding wheel. Commonly used binders can be divided into two categories: organic binders and inorganic binders, organic binders include resin binders and rubber binders, inorganic binders include ceramic binders, diamond binders and metal binders.
1. Resin bond grinding wheel: Generally, the most widely used cutting discs and grinding discs (except for some special grinding wheels) are used, and resin bond is used. The utility model is characterized by high bonding strength, convenient operation, good elasticity and good polishing effect. Because the resin is not resistant to high temperature, and the bonding agent is easy to burn out during use, the abrasive can contact the workpiece more. The grinding wheel not only ensures the sharpness of the grinding wheel, but also reduces the burnout of the workpiece. The firing temperature of the bonded grinding wheel is not as high as that of the ceramic grinding wheel, and the production time is short.
2. Rubber bond grinding wheel: The elasticity is greater than that of the resin bond, and the polishing performance is good. It is not easy to burn the workpiece during use, and is especially suitable for fine grinding or polishing processes. Synthetic rubber is generally used as a binder, with low firing temperature and short production cycle, but compact structure, small pores, and poor oil resistance. It is not suitable for general roughing and cannot be ground with oil-based grinding fluid.
3. Ceramic bond grinding wheel: mainly made of mineral products, similar to ceramics fired at high temperature, widely used, stable in chemical properties and good in heat resistance. In the process of processing, it is not affected by high temperature and the properties of the grinding fluid that change its composition, and its elastic deformation is small, and most of the grinding wheels are ceramic binders. However, since this bond must be sintered at high temperatures, the abrasive requirements are higher and the production cycle is longer.
4. Diamond bond grinding wheel: The casting manufacturing process is adopted, with few processes, and wet grinding wheels can also be produced, mainly by mixing abrasives in basic magnesium carbonate and magnesium chloride solutions. The mixture is then injected into a mold for curing. Its advantages are low calorific value during processing, but its disadvantages are low strength, poor water resistance and fast wear. Therefore, it is generally limited to tool polishing and other uses, and the scope of use is less.
5. Metal bond grinding wheel: It is mainly used to manufacture super-hard abrasive grinding wheel. Due to the high hardness of super-hard abrasive and the addition of metal bond, it can give full play to its advantages of sharpness and wear resistance. It is a kind of electroplating diamond roller sports equipment, which is made of several iron rods balancing and connecting two iron rings of the same size. The person climbs the pedals in the wheel, making the ring roll. Formerly known as Tiger V. Roller is also a common name for spare parts in the packaging machinery and beverage production industries, also known as roll sealing wheel, sealing wheel, and roll. The binder is mainly composed of copper, tin, iron and other materials, and the abrasive grains and the binder are combined (sintered) into high strength through powder metallurgy or electroplating process, so as to firmly control the abrasive grains and maintain the shape and strength of the grinding wheel. Extended service life
RELATED NEWS
2021-09-15
happy new year and congratulations
2021-09-15
Grinding wheel precision dressing
2021-09-15
Type of grinding wheel
2021-09-15
Grinding Wheel Safety Requirements
2021-09-15
Grinding wheel classification
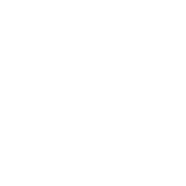

Inquiry